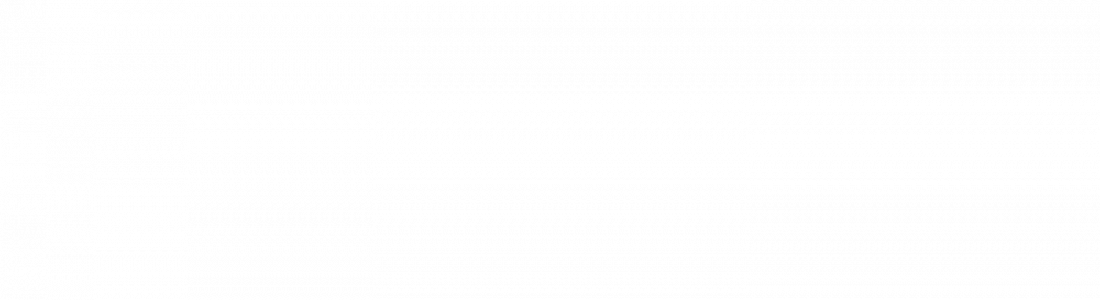
Why Is Nesting Optimization Important in Laser Cutting
In the realm of industrial laser cutting, efficiency is paramount. Every cut, every sheet of metal, and every operation must be optimized to minimize waste and maximize productivity.
One crucial aspect of this process is nesting optimization – the strategic arrangement of shapes and parts on a metal sheet to optimize material usage and minimize cutting time.
In this guide, we will delve into why nesting optimization is essential for laser cutting operations and explore best practices to enhance your nesting efficiency.
The Impact of Efficient Nesting
Efficient nesting can yield significant benefits across various dimensions of laser cutting operations:
Material Utilization: Optimized nesting ensures that every inch of the metal sheet is utilized effectively, reducing scrap and material wastage. This not only conserves resources but also lowers material costs, contributing to improved profit margins.
Space Optimization: By fitting more parts onto a single sheet, nesting optimization minimizes the storage space required for raw materials. This is particularly advantageous in facilities with limited space, allowing for more efficient inventory management and workspace utilization.
Reduced Production Time: When parts are arranged strategically, the laser cutter can traverse shorter paths, leading to reduced cutting time per sheet. This not only increases productivity but also extends the lifespan of laser cutting equipment by minimizing wear and tear.
Enhanced Quality Control: Efficient nesting reduces the likelihood of errors and defects during cutting, as parts are arranged in a manner that minimizes the risk of collisions and distortion. This improves overall product quality and reduces the need for rework or scrap.
Environmental Sustainability: By minimizing material waste and energy consumption, nesting optimization aligns with principles of sustainability and environmental responsibility. Manufacturers can reduce their carbon footprint and contribute to a greener future while maintaining operational efficiency.
Best Practices for Nesting Optimization
Achieving optimal nesting requires a combination of strategic planning, software utilization, and attention to detail.
Here are some best practices to enhance your nesting efficiency:
Utilize Advanced Nesting Software: Invest in advanced nesting software that utilizes algorithms to automatically arrange parts for optimal material usage. These programs consider factors such as part geometry, material constraints, and cutting parameters to generate efficient nesting layouts.
Consider Part Orientation: The orientation of parts on the metal sheet can significantly impact material utilization and cutting efficiency. Experiment with different orientations to minimize scrap and maximize the number of parts per sheet.
Account for Nesting Constraints: Take into account nesting constraints such as material grain direction, cutting sequence, and part nesting preferences. By adhering to these constraints, you can avoid issues such as warping, cutting errors, and inefficient use of material.
Optimize Nesting Order: Determine the optimal nesting order to minimize tool changes and traverse time for the laser cutter. Group similar parts together and arrange them in a sequence that minimizes unnecessary movements and maximizes cutting efficiency.
Regularly Review and Update Nesting Strategies: As production requirements and part designs evolve, periodically review and update your nesting strategies. By staying abreast of changes and continuously optimizing nesting layouts, you can maintain peak efficiency and competitiveness in the market.
QBuild Software – Engineering ERP Integration
Consider integrating your nesting data into your ERP System using QBuild Software’s powerful NESTLink Solution. By bridging the gap between your nesting software and ERP, NESTLink automates the creation of work orders from new job data pulled directly from your ERP system.
This seamless integration not only eliminates manual input processes but also ensures increased efficiency and data accuracy. With NESTLink, you can bid farewell to errors and delays, as it writes back to the ERP system after nesting and cutting operations, recording material and labor consumptions. Don’t miss out on the opportunity to streamline your workflow and optimize productivity.
Book a demo with us today and witness firsthand the transformative power of QBuild’s NESTLink Solution.
Book A Demo with QBuild Software today to explore cutting-edge solutions and take your laser cutting operations to new heights of efficiency and profitability.
Conclusion
In the competitive landscape of industrial manufacturing, efficiency reigns supreme. Nesting optimization stands as a cornerstone of efficiency in laser cutting operations, offering a pathway to cost reduction, resource conservation, and enhanced productivity.
By embracing best practices and leveraging advanced nesting software, manufacturers can unlock the full potential of their laser cutting processes, driving profitability and sustainability.
As you strive for excellence in your operations, remember that optimizing nesting isn’t just about cutting shapes – it’s about shaping a more efficient and sustainable future for your business.